Architectural and Automotive Glass
The design and manufacture of low-emissivity and solar control window coatings that improve both the energy efficiency and design aesthetic of buildings are the roots of our business. The equipment to deposit such coatings on large area glass substrates for the AGC Group is engineered, manufactured, and commercially deployed by the team of AGC Plasma Technology Solutions. The driving experience is changing rapidly in recent years with the development of electrical, autonomous, and connected vehicles. Magnetron sputtering technology underpins many of the new technologies deployed in these vehicles. Sputtering is used to produce solar control and low-emissivity coatings on the sunroof, anti-fog and heating functionality in the windshield, integrated antennas in the backlite, and anti-reflective treatment of curved display screens inside the car to improve readability with strong ambient light.
AGC Plasma Technology Solutions has been a pioneer in the field of glass coating equipment since deploying the first architectural glass coaters for the Interpane group in the early 1980s. Dozens of installations have been put into operation worldwide since then. The alliance between Interpane and AGC in 2012 brought together an expansive team of passionate PVD coating experts well experienced in the development of functionalized glass products, innovative PVD processes and manufacturing equipment, and in ensuring the operational excellence in multiple coating production plants.
The horizontal coater is widely used as a standard tool for depositing low-emissivity and solar control coatings on large area glass substrates for building and automotive applications. The ability to coat substrates of up to 3.2 meters x 6 meters in size makes it well-suited for producing coated glass panels used in windows, facades, and automotive glazing.
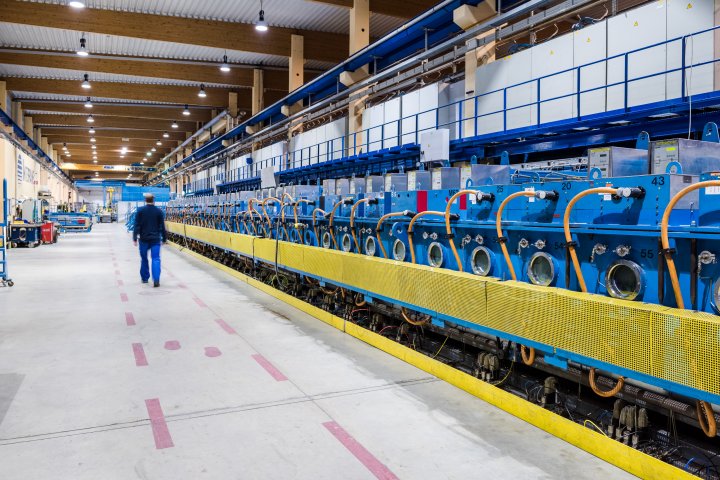
Key advantages of such coaters for large area glass substrates include high throughput, superior coating uniformity, and an optimized total cost of ownership.
AGC developed a method for partial coating on automotive glass substrates by applying a removable mask prior to going through the coating line. This method allows for selective coatings on specific areas of the glass substrate, leaving other areas uncoated. The partial coating approach is often used for automotive applications where certain areas of the glass require transparency for sensors that are installed behind the windshield. Alternatively, the coating can be removed by laser ablation on specific areas after the coating deposition.
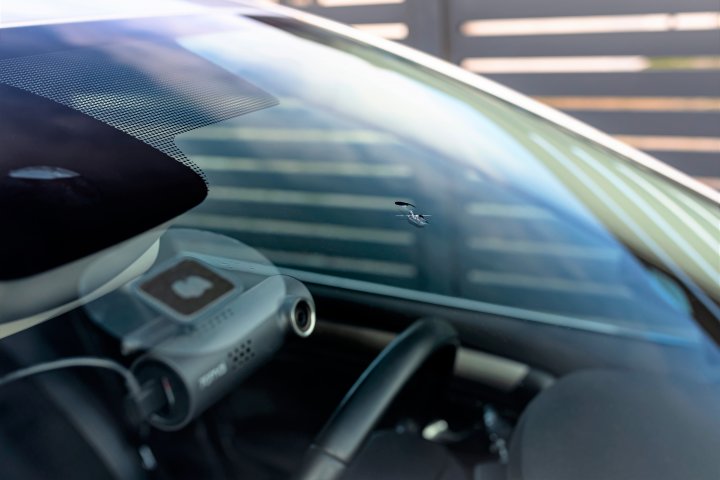
A major challenge in large-area coating is achieving uniformity across the entire width of the substrate. Non-uniformities in the coating can result in variations in optical properties, which can affect the performance and appearance of the final product. AGC's iOSMB technology addresses this challenge by compensating for non-uniformities in the profile of the deposited coating without the need to switch off the plasma or to vent the coater, which interrupts the production process. The iOSMB is a magnet bar located inside the rotatable cathode and it controls the magnetic field strength distribution in real time during the coating process. By controlling the magnetic field strength, the iOSMB technology compensates for variations in the coating process, such as changes in plasma density or deposition rate, and ensures that the coating is deposited uniformly across the entire width of the substrate.
The result is a remarkable improvement in coating uniformity, with non-uniformities limited to +/- 0.3% over the coating width for dielectric and metal layers. In addition, upgrading coating equipment with the iOSMB technology strongly reduces the tuning time of the coating process during start-up, as it is more straightforward to use compared to gas trimming.
Features
- High-throughput coating line relies on AGC's industrially proven magnetron sputtering (PVD) technology with superior process stability and reproducibility
- Highest quality coatings
- Low particle pollution and coating uniformity unmatched in industry
- Custom-engineered sample holders to optimize line coverage and maximize machine output
- Coating line equipped with automated carrier return system hosted in a clean room to avoid dust contamination
- Modular and flexible equipment design easily allows future system upgrades
- Quick switch-over times between different coatings maximizes machine uptime
- Substrate pre-cleaning and quality control equipment integrated into system for turnkey operation
- User-friendly operating system and easy maintenance
- Remote access possible for quick troubleshooting by AGC support team